In recent years, we have witnessed a surge in the use of off-site construction methods, particularly in residential construction. Two methods that have gained considerable attention are volumetric and panelised construction. Both approaches offer distinct advantages, and we want to share why we believe panelised construction emerges as the preferred choice for low-rise housing projects.
First, let’s briefly review the difference between the two methods. Volumetric construction involves assembling three-dimensional modules or units off-site, which are then transported to the building site and lifted into position to form the structure. On the other hand, panelised construction entails creating individual panels off-site, which are then transported to the site and assembled to construct the three-dimensional building.
1. Cost-Efficiency
Modular buildings in particular have higher costs associated with them as they are often over-engineered to ensure the modular construction reaches site safely and intact. Housing Associations may accept these costs to provide affordable housing quickly, but national house builders might not prioritise speed as much, and therefore consider the added costs unnecessary.
The manufacturing process of panelised systems allows for better cost control and is more cost-effective due to less onerous lifting, easier handling and transportation requirements, and reduced labour and material expenses involved in the manufacturing stages.
2. Faster Construction Timeline
Both methods of construction present speed of delivery, but panelised methods limit the risk of error by manufacturing components in parallel with on-site preparation. This results in reduced construction periods, enabling developers to complete projects on time and even ahead of schedule. If an error occurs in modular building, the bulk of the build process is likely to have already been completed, so it can be costly and disruptive to fix.
An Intrastack framed building can be constructed up to 50% faster than a traditional structure, leading to reduced site preliminaries, reduced plant costs, and an earlier ROI. And, due to the nature of off-site construction, light gauge steel frame systems (LGSF) in particular are less reliant on weather conditions and have a much easier installation process.
3. Enhanced Quality Control
Both methods allow for meticulous quality control. They are produced in a controlled environment, minimising the impact of adverse weather conditions, and ensuring consistency in build quality. Additionally, the use of advanced technologies in the fabrication process ensures precision and accuracy, reducing the likelihood of errors.
The accuracy and precision of LGSF technology (up to 1mm per structural storey height), allows for a more exacting interface with finishing systems, leading to higher levels of quality and performance.
4. Flexibility and Customisation
The aim for low-rise housing is to create visually captivating neighbourhoods that cater to the needs of residents, necessitating diverse designs and orientations. Achieving a more intricate design in residential construction might prove challenging with modular boxes as they have limitations due to transportation constraints. This often leads to a boxy internal layout of typically longer, narrow rooms. Unlike our light gauge steel frame system, which offers greater flexibility.
Assembling individual panels allows for easier integration of unique features and architectural elements. This offers architects and builders more freedom to customise and modify building designs whilst maintaining key design-parameters to ensure manufacturing and installation efficiencies and ensuring overall commerciality.
5. Decision-Making
One crucial aspect that sets panelised construction apart from volumetric is the timing of decision-making for design and finishes. For modular buildings, these decisions must be made upfront, as any alterations or changes during the production phase can disrupt the entire process and lead to delays.
On the other hand, panelised construction offers greater flexibility in decision-making regarding fixtures, fittings, and finishings. During the on-site build stage, more cosmetic decisions can still be made, allowing for adjustments and refinements as needed.
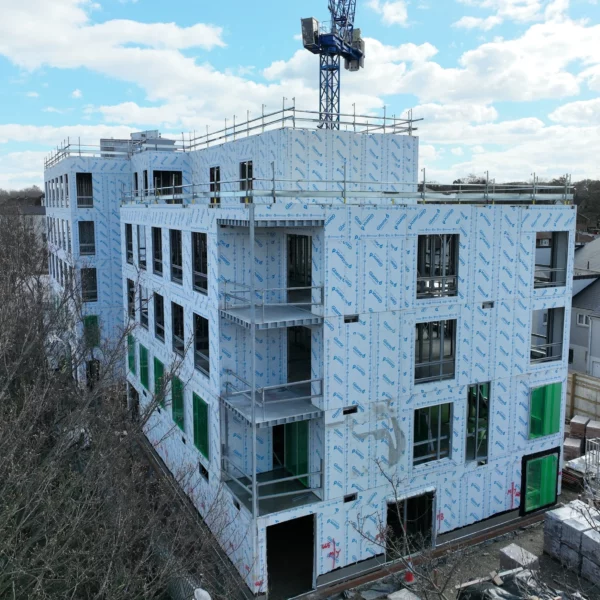
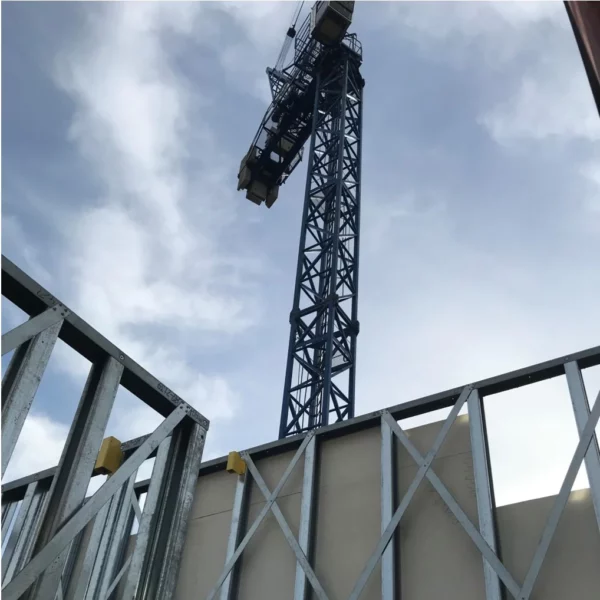
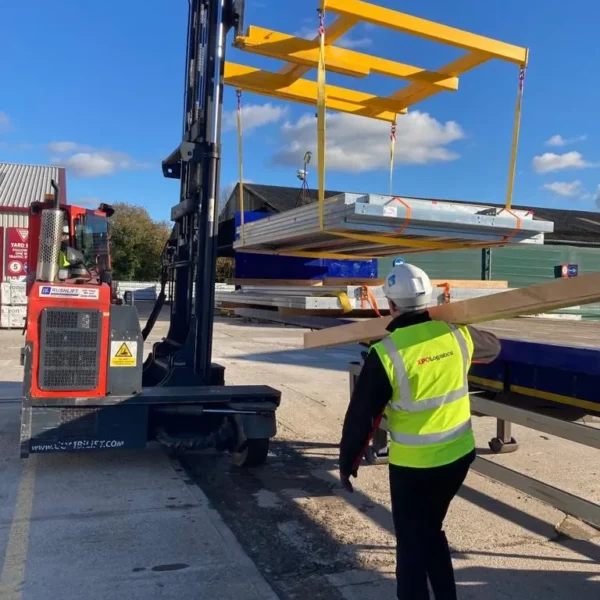
6. Improved Safety Standards
Both methods of construction contribute to a safer work environment. The majority of the manufacturing process occurs in a controlled factory setting, which reduces the risks associated with on-site construction.
When using pre-panellised LGSF structures the HSE states that site safety is improved by a factor of 5 through the reduction in site labour, reduced working-at-height and less waste on-site (trip hazards). Consequently, this minimises the likelihood of accidents and injuries for workers and visitors alike.
7. Financial Considerations and Government Incentives
Unlike panelised systems, embarking on a modular building project necessitates a substantial initial investment, as the entire house is constructed in the factory before receiving payment. This is especially true for large residential developments, where the upfront costs per unit can quickly add up, becoming a significant financial undertaking.
Both methods of residential construction can also present opportunities for financial incentives. By meeting the government’s strategic partnership grant requirement of reaching a 55% premanufactured value (PMV) threshold, projects can benefit from governmental support. Panelised systems also have the potential to well exceed this threshold by incorporating elements like closed panel construction, staircases, roofs, or bathroom pods.
8.Reliable partnerships
Long-standing brands, like Saint-Gobain who has 350-years of experience, possess a comprehensive understanding of construction from a manufacturing standpoint. They can effectively strike a balance between commercial considerations and sustainable practices, which is key in this industry.
It’s important to work with reliable, long-standing manufacturers that can advise on methods of construction and efficient design for your specific project and see the project through to completion.
9. Fire Protection
In terms of fire resistance, both panelised and modular construction can be designed to meet fire safety standards by using fire-resistant materials, insulation, and fire barriers. Additionally, both methods must adhere to local building codes and regulations, which often include fire safety requirements.
Intrastack light gauge steel frame structures can offer up to 120 minutes fire performance based on our tested configurations. All of our solutions are fully non-combustible, providing additional benefit to the construction site in regard to fire-mitigation requirements during construction.
In conclusion…
While volumetric and panelised construction both offer innovative solutions for low-rise housing, it is evident that panelised construction presents a more favourable option. Its cost-effectiveness, ensuring a faster construction timeline than traditional methods, enhanced quality control, design flexibility, and improved safety standards collectively contribute to making it an optimal choice for builders and developers within the private and public housing sectors.
Contact us today to learn more about how we can help with your next panelised construction project.